Сегодня технология низкотемпературной керамики (LTCC – Low Temperature Co-fired Ceramics) быстро развивается и успешно применяется для различных приложений – телерадиовещания, телекоммуникаций, мобильной связи, портативных компьютеров, производства ВЧ- и СВЧ-микросхем низкой и средней степени интеграции и др. Развитие глобальных сетей вызвало повышенный интерес к LTCC-технологии. И в первую очередь это относится к высокочастотным модулям обмена данными с их высокой степенью интеграции, небольшими размерами компонентов и, конечно, предельными рабочими параметрами. LTCC-технология – это недорогое решение для массового производства электронных устройств, применяемых в коммерческой и военной областях радиоэлектронной промышленности.
Стремительное развитие индустрии мобильных телефонов и портативных компьютеров, совершенствование технологий приема/передачи текстовых и графических сообщений привели к тому, что широкополосную связь и высокочастотные технологии стали очень активно применять на практике. Работая на волнах 800 МГц, 1,5 ГГц и 2 ГГц, мобильная связь осваивает более высокие частоты: Bluetooth – 2,45 ГГц для беспроводной LAN, ETC – 5,3 ГГц. На частотах порядка 10 ГГц и более планируется внедрить WLL (Wireless Local Loop, 20–30 ГГц) и автомобильные радары (50–140 ГГц, 76 ГГц – наиболее перспективная частота) [1]. LTCC-технология – одна из наиболее перспективных с точки зрения СВЧ-применений.
Основные достоинства LTCC-технологии:
более экономичное производство по сравнению с традиционной толстопленочной технологией;
возможность проектирования и производства ЗD-контуров;
возможность вырезания ленты/подложки любой формы;
число рабочих слоев не ограничено;
возможность размещения пассивных компонентов внутри подложки, что уменьшает размер контуров более чем на 50% по сравнению с печатными платами;
хорошая теплопроводность по сравнению с печатными платами;
рабочие частоты свыше 30 ГГц;
рабочие температуры до 350°С;
температура обжига порядка 850°С позволяет применять материалы с малым удельным сопротивлением, такие как золото и серебро, вместо молибдена и вольфрама, используемых в высокотемпературной технологии;
каждый слой инспектируется до сборки модуля и при необходимости может быть заменен, что повышает процент выхода годных изделий;
отличная герметизация слоев;
технологический цикл производства многослойных керамических модулей экологически чист и компактен;
отсутствие химических процессов;
многие процессы при серийном производстве можно автоматизировать;
сокращение производственных циклов по сравнению с обычными толстопленочными технологиями.
Приведем краткий обзор основных и вспомогательных материалов, которые наиболее часто используются в данной технологии (табл.1).
LTCC сравнительно просто сочетается с материалами, имеющими различные характеристики, что позволяет интегрировать и создавать различные типы компонентов на основе керамики. Более того, так как LTCC имеет низкие диэлектрические потери при высоких частотах, а в качестве проводников применимы металлы с низкими потерями, то можно создавать эффективные системы с малыми потерями и лучшими диэлектрическими характеристиками по сравнению с традиционными системами на основе смол (табл.2).
Из табл.2 видно, что tg δ LTCC в три раза меньше, чем у FR 4 и, соответственно, предпочтительнее для использования в СВЧ-технике.
Первый и, безусловно, наиболее сложный процесс в LTCC-технологии – это подготовка керамической суспензии (шликера). Процесс включает в себя подбор сырья и его предварительную обработку (термическую, химическую, механическую), а также выбор связующих. Сегодня российские производители керамического сырья в большей степени ориентированы на "грубое" применение своей продукции (например, в строительстве или производстве посуды). Поэтому, чтобы получить стабильные составы LTCC-керамики, а значит, качественный конечный продукт, необходим тщательный входной контроль материалов. При изготовлении шликера для LTCC используют множество органических материалов для смешивания с неорганическим керамическим сырьем – это связующие материалы, пластификаторы, диспергирующие добавки и растворители.
Когда список необходимых материалов сформирован, а сами они взвешены, их смешивают в шаровой мельнице ("ball mill) или на аналогичном оборудовании. Рассмотрим более подробно особенности получения шликера. Основные типы LTCC-керамики – это стеклокерамические композиты и кристаллическое стекло, и для каждого из них используются разные дополнительные материалы.
Для создания стеклокерамического композита применяют два типа неорганического порошка (керамический и стеклянный), причем обязательным условием является минимальная разница в величине поверхностного заряда основного и вспомогательного материалов. В противном случае произойдет агрегирование данных материалов. При подборе диаметра частиц и общей площади поверхности порошка (рис.1) необходимо уделить внимание количеству связки для формовки и текучести стекла при отжиге. Если диаметр гранул порошка относительно мал, а, соответственно, общая площадь поверхности всех гранул велика, то следует увеличить количество связующего вещества. Но с увеличением содержания связующего материала в процессе отжига (обязательный процесс в технологии LTCC) увеличится и его усадка. Поэтому, если усадка – критичный параметр, то лучше создавать порошок на основе частиц с большим диаметром. Важна также способность стекла компенсировать неоднородности частиц керамики в процессе отжига. Таким образом, в зависимости от назначения конечного продукта можно задать его характеристики (например, плотность и усадку) после термообработки, выбрав диаметр частиц. И, естественно, чем более однороден состав порошков по размеру и форме, тем более качественный продукт получается после отжига.
В случае с кристаллическим стеклом используется только один вид керамического порошка, поэтому зарядовые характеристики материала не важны. Однако для получения однородной структуры нужно, чтобы частицы были идеально распределены по форме и размеру. В данном случае необходимо только подобрать размер гранул и общую площадь поверхности, c учетом их способности к формованию и отжигу [2].
В производстве LTCC используются хорошо известные органические материалы:
связки (для поддержания прочности при формовке);
пластификаторы (обеспечивают реологические свойства шликера и придают пластичность отлитой керамике);
диспергирующие агенты (добавки, которые контролируют рН шликера и поверхностный заряд частиц, а также являются пространственным барьером между частицами и в то же время – растворителями агломерирующих частиц);
противопенные добавки (для предотвращения вспенивания шликера);
поверхностно активные вещества ПАВ – для увеличения низкой смачиваемости керамического порошка посредством снижения поверхностного натяжения;
безводные органические растворители.
В основном эти органические материалы используются для задания характеристик промежуточных продуктов – шликера, "зеленой" ленты, "зеленых" ламинированных объектов. Но на стадии отжига все органические составляющие должны быть удалены из конечного продукта, поэтому желательно использовать их в минимальном количестве. Традиционные органические материалы, используемые в LTCC-технологии, представлены в табл. 3 и 4 [3, 4].
Помимо грамотного и качественного подбора дополнительных материалов также важна и последовательность их смешивания. Надо сказать, что при организации производства LTCC-керамики в штате специалистов должны быть профессиональные химики. Хотя есть и готовые решения – существует ряд компаний, которые занимаются исключительно разработкой шликеров на основе стандартных материалов. Традиционно, чтобы обеспечить максимальную сочетаемость материалов "в технологии РЭА", шликер разрабатывается совместно с пастой для нанесения топологий проводников. Стандартные процессы изготовления и пример LTCC-компонента приведены на рис.2–4.
Число предприятий, проявляющих интерес к технологии LTCC, за 2009 год значительно выросло по сравнению с предыдущими годами. Об этом говорят проведенные мероприятия (семинары, конференции, выставки), посвященные как конкретно данной технологии, так и СВЧ-технике в целом. В ближайшее время LTCC будет все активнее применяться в спецтехнике и в коммерческой аппаратуре. Представленный обзор материалов и процесса приготовления шликера краткий и написан для ознакомления с некоторыми нюансами и сложностями технологии. Это первая статья из цикла статей о конкретных процессах технологии LTCC, планируемых Предприятием Остек для публикации.
Литература
1. Development of Ubiquitous Service using Wireless Technology, NTT. – Technical Journal, 2003, № 3, p. 6–12.
2. Imanaka Y. Multilayered Low Temperature Cofired Ceramics (LTCC) Technology, Springer Science+Business Media, Inc. (2005), p.103–104.
3. Mistler R.E. Tape Casting. – The Basic Process for Meeting the Needs of the Electronic Industry, Ceramic Bull., 1990, vol. 69, № 6, p. 1022–1026.
4. Saito K. Use of Organic Materials for Ceramic-Modeling Process-Binder, Deffloculant, Plasticizer, Lubricant, Solvent,
Основные достоинства LTCC-технологии:
более экономичное производство по сравнению с традиционной толстопленочной технологией;
возможность проектирования и производства ЗD-контуров;
возможность вырезания ленты/подложки любой формы;
число рабочих слоев не ограничено;
возможность размещения пассивных компонентов внутри подложки, что уменьшает размер контуров более чем на 50% по сравнению с печатными платами;
хорошая теплопроводность по сравнению с печатными платами;
рабочие частоты свыше 30 ГГц;
рабочие температуры до 350°С;
температура обжига порядка 850°С позволяет применять материалы с малым удельным сопротивлением, такие как золото и серебро, вместо молибдена и вольфрама, используемых в высокотемпературной технологии;
каждый слой инспектируется до сборки модуля и при необходимости может быть заменен, что повышает процент выхода годных изделий;
отличная герметизация слоев;
технологический цикл производства многослойных керамических модулей экологически чист и компактен;
отсутствие химических процессов;
многие процессы при серийном производстве можно автоматизировать;
сокращение производственных циклов по сравнению с обычными толстопленочными технологиями.
Приведем краткий обзор основных и вспомогательных материалов, которые наиболее часто используются в данной технологии (табл.1).
LTCC сравнительно просто сочетается с материалами, имеющими различные характеристики, что позволяет интегрировать и создавать различные типы компонентов на основе керамики. Более того, так как LTCC имеет низкие диэлектрические потери при высоких частотах, а в качестве проводников применимы металлы с низкими потерями, то можно создавать эффективные системы с малыми потерями и лучшими диэлектрическими характеристиками по сравнению с традиционными системами на основе смол (табл.2).
Из табл.2 видно, что tg δ LTCC в три раза меньше, чем у FR 4 и, соответственно, предпочтительнее для использования в СВЧ-технике.
Первый и, безусловно, наиболее сложный процесс в LTCC-технологии – это подготовка керамической суспензии (шликера). Процесс включает в себя подбор сырья и его предварительную обработку (термическую, химическую, механическую), а также выбор связующих. Сегодня российские производители керамического сырья в большей степени ориентированы на "грубое" применение своей продукции (например, в строительстве или производстве посуды). Поэтому, чтобы получить стабильные составы LTCC-керамики, а значит, качественный конечный продукт, необходим тщательный входной контроль материалов. При изготовлении шликера для LTCC используют множество органических материалов для смешивания с неорганическим керамическим сырьем – это связующие материалы, пластификаторы, диспергирующие добавки и растворители.
Когда список необходимых материалов сформирован, а сами они взвешены, их смешивают в шаровой мельнице ("ball mill) или на аналогичном оборудовании. Рассмотрим более подробно особенности получения шликера. Основные типы LTCC-керамики – это стеклокерамические композиты и кристаллическое стекло, и для каждого из них используются разные дополнительные материалы.
Для создания стеклокерамического композита применяют два типа неорганического порошка (керамический и стеклянный), причем обязательным условием является минимальная разница в величине поверхностного заряда основного и вспомогательного материалов. В противном случае произойдет агрегирование данных материалов. При подборе диаметра частиц и общей площади поверхности порошка (рис.1) необходимо уделить внимание количеству связки для формовки и текучести стекла при отжиге. Если диаметр гранул порошка относительно мал, а, соответственно, общая площадь поверхности всех гранул велика, то следует увеличить количество связующего вещества. Но с увеличением содержания связующего материала в процессе отжига (обязательный процесс в технологии LTCC) увеличится и его усадка. Поэтому, если усадка – критичный параметр, то лучше создавать порошок на основе частиц с большим диаметром. Важна также способность стекла компенсировать неоднородности частиц керамики в процессе отжига. Таким образом, в зависимости от назначения конечного продукта можно задать его характеристики (например, плотность и усадку) после термообработки, выбрав диаметр частиц. И, естественно, чем более однороден состав порошков по размеру и форме, тем более качественный продукт получается после отжига.
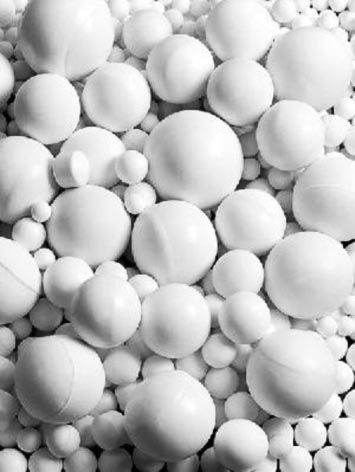
Рис.1. Исходный порошок алюмооксидной керамики
В случае с кристаллическим стеклом используется только один вид керамического порошка, поэтому зарядовые характеристики материала не важны. Однако для получения однородной структуры нужно, чтобы частицы были идеально распределены по форме и размеру. В данном случае необходимо только подобрать размер гранул и общую площадь поверхности, c учетом их способности к формованию и отжигу [2].
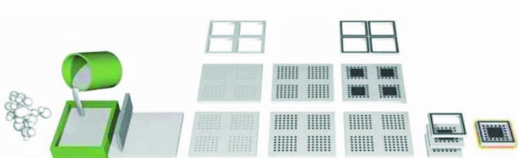
Рис.2. Стандартный маршрут изготовления LTCC компонентов (последовательность процессов: подготовка шликера; отливка керамики; резка на карты; пробивка отверстий и окон; заполнение отверстий и формирование топологии проводников; сборка в стек; изостатическ
В производстве LTCC используются хорошо известные органические материалы:
связки (для поддержания прочности при формовке);
пластификаторы (обеспечивают реологические свойства шликера и придают пластичность отлитой керамике);
диспергирующие агенты (добавки, которые контролируют рН шликера и поверхностный заряд частиц, а также являются пространственным барьером между частицами и в то же время – растворителями агломерирующих частиц);
противопенные добавки (для предотвращения вспенивания шликера);
поверхностно активные вещества ПАВ – для увеличения низкой смачиваемости керамического порошка посредством снижения поверхностного натяжения;
безводные органические растворители.
В основном эти органические материалы используются для задания характеристик промежуточных продуктов – шликера, "зеленой" ленты, "зеленых" ламинированных объектов. Но на стадии отжига все органические составляющие должны быть удалены из конечного продукта, поэтому желательно использовать их в минимальном количестве. Традиционные органические материалы, используемые в LTCC-технологии, представлены в табл. 3 и 4 [3, 4].
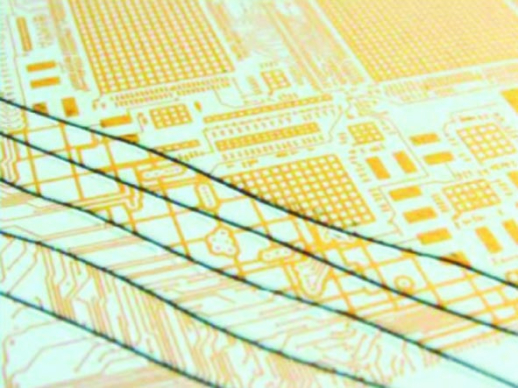
Рис.3. Пример листов "зеленой" керамики с нанесенной топологией
Помимо грамотного и качественного подбора дополнительных материалов также важна и последовательность их смешивания. Надо сказать, что при организации производства LTCC-керамики в штате специалистов должны быть профессиональные химики. Хотя есть и готовые решения – существует ряд компаний, которые занимаются исключительно разработкой шликеров на основе стандартных материалов. Традиционно, чтобы обеспечить максимальную сочетаемость материалов "в технологии РЭА", шликер разрабатывается совместно с пастой для нанесения топологий проводников. Стандартные процессы изготовления и пример LTCC-компонента приведены на рис.2–4.
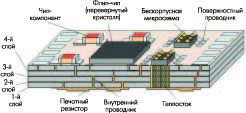
Рис.4. Пример компонента, изготовленного по технологии LTCC
Число предприятий, проявляющих интерес к технологии LTCC, за 2009 год значительно выросло по сравнению с предыдущими годами. Об этом говорят проведенные мероприятия (семинары, конференции, выставки), посвященные как конкретно данной технологии, так и СВЧ-технике в целом. В ближайшее время LTCC будет все активнее применяться в спецтехнике и в коммерческой аппаратуре. Представленный обзор материалов и процесса приготовления шликера краткий и написан для ознакомления с некоторыми нюансами и сложностями технологии. Это первая статья из цикла статей о конкретных процессах технологии LTCC, планируемых Предприятием Остек для публикации.
Литература
1. Development of Ubiquitous Service using Wireless Technology, NTT. – Technical Journal, 2003, № 3, p. 6–12.
2. Imanaka Y. Multilayered Low Temperature Cofired Ceramics (LTCC) Technology, Springer Science+Business Media, Inc. (2005), p.103–104.
3. Mistler R.E. Tape Casting. – The Basic Process for Meeting the Needs of the Electronic Industry, Ceramic Bull., 1990, vol. 69, № 6, p. 1022–1026.
4. Saito K. Use of Organic Materials for Ceramic-Modeling Process-Binder, Deffloculant, Plasticizer, Lubricant, Solvent,
Отзывы читателей