Особенности трафаретной печати и сборки в стек на оборудовании КЕКО
Принтер-стекер PAL-9Y (рис.1) используется в основном для производства пассивных компонентов, таких как многослойные керамические конденсаторы (MLCC). При разработке компонентов и выборе оборудования необходимо помнить, что точность окончательной сборки определяется "точностью позиционирования" оборудования и особенностями материалов и технологий. Понятие "точность позиционирования" включает в себя повторяемость позиционирования одиночной палетты носителя; повторяемость сдвига трафарета; параллельность и плоскостность прессовальной плиты; механическую повторяемость прочих параметров с минимальным влиянием на точность процесса печати.
На точность окончательной сборки влияют трафарет, параметры процесса печати, паста, керамическая лента.
Влияние трафарета на процесс печати. На большинстве производств сегодня используют сетко-трафареты 325 и 400 меж (число ячеек на дюйм), которые выбираются в зависимости от конечного продукта. На качество нанесения рисунка в основном влияют окно сетки, толщина проводника и способ изготовления трафарета. Если использовать трафареты, выполненные с помощью фотоэмульсии, то невозможно получить ровные края проводника (рис.2). Для трафарета 325 меж неровность края ("зигзаг") составляет от 20 до 30 мкм, для трафарета 400 меж – 5–10 мкм.
При изготовлении трафаретов с использованием фоточувствительных пленок этот эффект отсутствует, но такие трафареты в основном непригодны для тонких рисунков за счет дополнительной толщины пленки. При сборке стека эффект "зигзага" при использовании качественного трафарета не имеет значительного влияния на позиционирование. В технологическом процессе это называется виртуальной разориентацией, которую необходимо учитывать, если требуется точность порядка нескольких микрон. При выполнении трафаретной печати существует еще одна проблема – удлинение трафарета в направлении движения ракеля (рис.3).
Эффект удлинения трафарета приводит к тому, что окончательный рисунок имеет большие размеры и сдвигается в направлении печати по сравнению с исходным (рис.4).
На изменение длины трафарета влияют:
окно сетки (больше окно, больше удлинение);
размеры рамки трафарета (больше рамка, больше удлинение);
площадь печати (больше площадь, больше удлинение);
натяжение трафарета (новые трафареты – меньше удлинение, использованные – больше удлинение);
однородность натяжения трафарета (определяет форму удлинения);
тип ракеля (полиуретановый или алмазный, полиуретановый меньше и более однородное удлинение);
усилие на ракель (большее усилие, больше удлинение);
линейность рабочей части ракеля (влияет на форму удлинения);
параллельность ракеля плоскости печати (влияет на форму удлинения).
Если трафарет выполнен на пленке, то удлинение незначительное, если же на эмульсии, то большое.
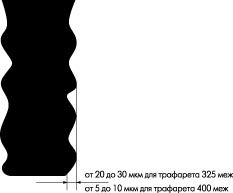
Стандартное удлинение трафарета составляет примерно 100 мкм для трафаретной рамки размером 450×450 с площадью рисунка 6×6 дюймов. Эффект удлинения трафарета также линейно зависит от плошади наносимого рисунка (больше площадь, больше удлинение). Данный эффект оказывает меньшее влияние на позиционирование единичного чип-компонента в процессе групповой обработки, если направление печати одинаковое для всех подложек в партии, параметры печати не меняются в течение технологического цикла, печать осуществляется одним ракелем. Удлинение трафарета оказывает значительное влияние на точность нанесения топологии, во-первых, если два трафарета использовались в одном технологическом цикле, и, во-вторых, если осуществлялось нанесение топологии в несколько этапов с поворотом трафарета или подложки. В последнем случае эффект удлинения удваивается. Его можно частично устранить смещением центра трафарета относительно центра подложки в противоположную сторону от направления удлинения. Так как удлинение неоднородно по всему трафарету, то невозможно идеально наложить два рисунка с поворотом. В случае изготовления конденсаторов поворот можно заменить рядом иных технологических приемов. При использовании двойной печати в противоположных направлениях рисунок тоже смещается в двух направлениях и в результате увеличивается площадь печати.
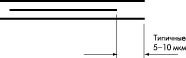
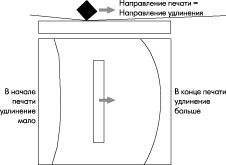
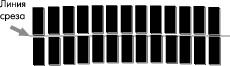
Удлинение трафарета приводит также к проблемам при изготовлении компонентов малого размера на большой площади печати, так как линии печатных элементов будут искривлены. При резке на конечные элементы это приведет к возникновению брака (рис.5).
Влияние паст на процесс печати. Паста не должна высыхать на трафарете в процессе печати. Если она сохнет быстро, то будет оставаться на боковых поверхностях рисунка трафарета. При этом возникает необходимость часто чистить трафарет. В противном случае после очистки площадь печати будет больше. В результате имеем, что быстрое высыхание и частая очистка трафарета приводят к возникновению неравномерности печати. И рисунок меняется от процесса к процессу. Печатная паста считается подходящей, если нет необходимости чистить трафарет при его длительном использовании.
Печатная паста должна быстро высыхать при низких температурах. Высокие температуры (выше 800°С) и длительное время (более 4 мин) сушки приводят к удлинению носителя (ленты, палетты), керамической ленты и, как следствие, к возможному искажению рисунка.
Влияние керамической ленты на процесс печати. Совместимость свойств ленты с процессом укладки в стек является важнейшим моментом при осуществлении позиционирования и прессования. На совместимость с процессами печати и стекирования оказывает влияние проницаемость ленты. В процессе укладки последующего листа к предыдущему в стек низкая проницаемость ленты приводит к возникновению между листами полостей с воздухом, что является дефектом (рис.6). Проницаемость керамической ленты на майларе должна иметь лучшую проницаемость по сравнению с лентой без пленки-носителя. Обычно уменьшая содержание связки и пластификатора в ленте, можно повысить ее проницаемость.
Параметры захвата ленты тоже влияют на качество трафаретной печати, поэтому сила захвата ленты должна быть менее 10 Н/мм2 для лент на майларе и 5 Н/мм2 для лент без майлара; температура захвата до 800°С. Более высокие температуры и усилия могут привести к деформации стека, если свойства ленты неточно подобраны. Большинство применяемых лент позволяют работать в требуемом диапазоне параметров, исключая некоторые ленты на водной основе для которых необходимо подбирать параметры захвата.
Условия деформации ленты. Некоторые ленты с большим содержанием пластификатора подвержены деформации при приложении давления и температуры. Деформация выражается в сдвиге и изменении формы стека. Растяжение стека приводит к сильному удлинению (подобные проблемы имеет большинство лент компании Ferro, выполненных по стандартной формуле). Для получения хорошего результата удлинение ленты должно быть минимальным (меньше 5% до разрыва ленты). Условия деформации ленты наиболее критичны при использовании органических связок в отличие от лент на водной основе, которые более устойчивы к искажениям.
Пластичность ленты. Данная характеристика так или иначе связана с деформацией. Лента должна обладать достаточной пластичностью, чтобы в процессе укладки в стек устранить возможные отклонения толщины ленты. Если часть ленты толще другой на 1 мкм, то разница стека в 100 слоев по толщине составит 100 мкм. Эта неоднородность компенсируется локальной деформацией ленты.
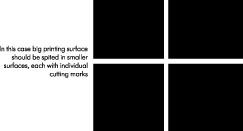
Большинство "зеленых" лент, созданных на основе органических связок, обладают данным свойством в отличие от лент на водной основе без необходимых добавок.
Из опыта работы Предприятия ОСТЕК примерно 80% материалов пригодно для использования на машине типа PAL-9 (а также на всех машинах производства KEKO Equipment, предназначенных для выполнения данных задач), особенно, если в качестве поставщика материала выбраны крупные компании, например, Ferro, DuPont, Heraeus и др.
ЗАО Предприятие Остек – инжиниринговая компания, эксклюзивный представитель (поставка, установка и сервисное обслуживание оборудования) многих зарубежных компаний, производящих высокотехнологичное оборудование, в том числе и КЕКО Equipment. Российским производителям электроники предлагается как единичное оборудование, так и комплексные решения для предприятий любого уровня.